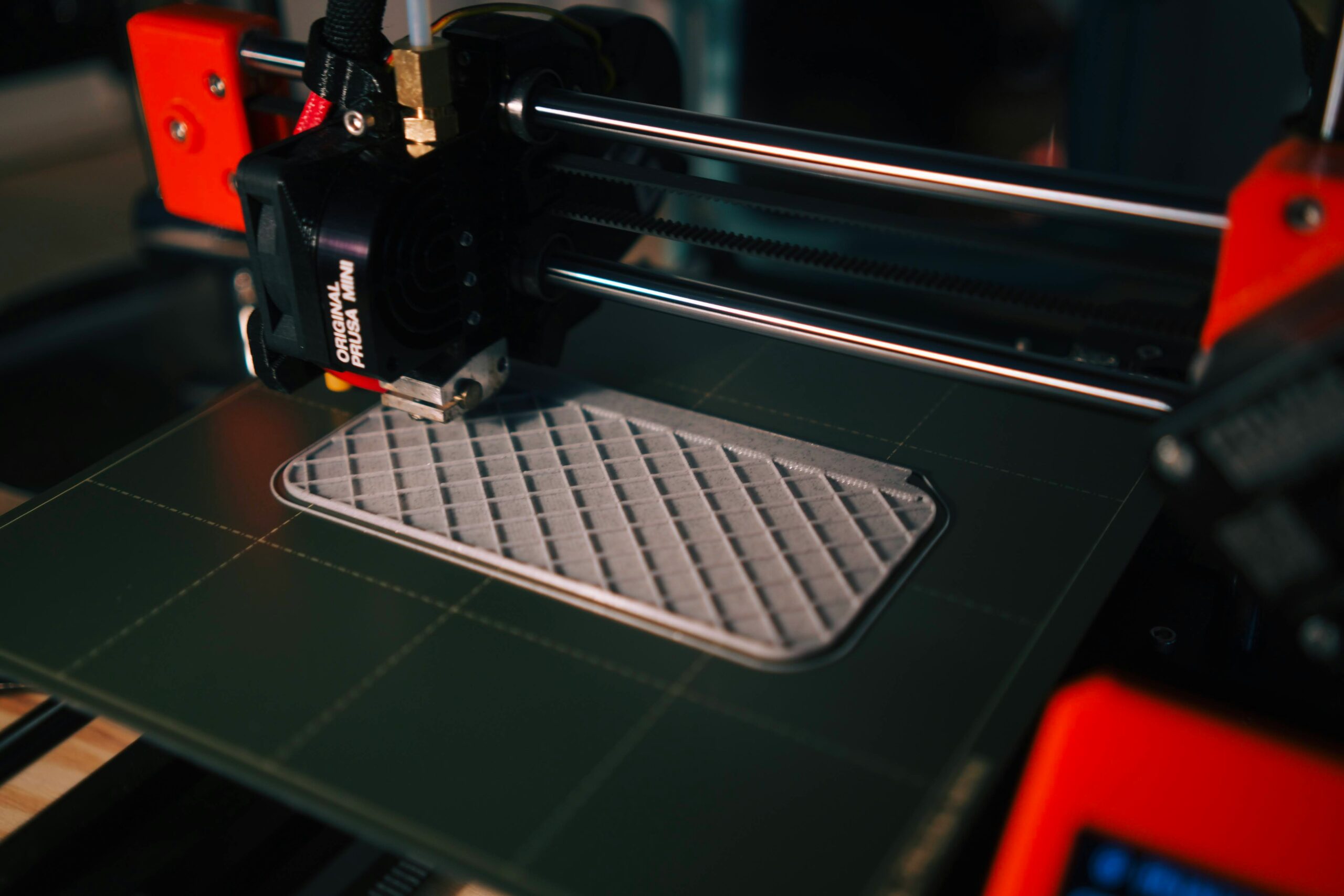
Introduction to 3D Printing Materials
The advent of 3D printing has revolutionized various industries by enabling the creation of complex geometries and customized designs. At the heart of this innovative technology lies the choice of materials, which plays a critical role in determining the performance, durability, and quality of the finished product. As 3D printing technology has advanced, the variety of available materials has expanded significantly, catering to diverse applications ranging from prototyping to final production.
Initially, 3D printing primarily utilized thermoplastics such as acrylonitrile butadiene styrene (ABS) and polylactic acid (PLA). These materials marked the early days of additive manufacturing, offering simplicity and ease of use for hobbyists and engineers alike. However, as the technology progressed, there emerged a demand for materials that could withstand more rigorous conditions, leading to the introduction of specialty filaments and powders such as nylon, TPU (thermoplastic polyurethane), and metal composites. Today, the ecosystem of 3D printing materials includes not only plastics but also metals, ceramics, and bio-based substances, each tailored for specific applications.
The selection of the appropriate 3D printing material is crucial, as it impacts various factors such as mechanical properties, thermal resistance, and surface finish. Different projects require distinct characteristics; for example, a functional prototype may necessitate materials that provide higher strength and flexibility, while an aesthetic model might prioritize visual appeal instead. Understanding the properties and requirements of various materials ensures that designers and engineers can achieve their desired outcomes, enhancing both the functionality and appearance of their final products. Ultimately, as 3D printing continues to evolve, so too will the range of materials available, presenting exciting possibilities for innovation across various fields.
Common 3D Printing Materials and Their Properties
3D printing has revolutionized various industries by allowing for the creation of complex geometries with an array of materials. Understanding the common 3D printing materials is essential for selecting the right one for your project. Among the most popular materials are PLA, ABS, PETG, Nylon, TPU, and Resin, each possessing distinct properties that cater to different needs.
PLA (Polylactic Acid) is one of the most widely used materials in 3D printing due to its ease of use and environmental friendliness, being derived from renewable resources like cornstarch. PLA is biodegradable and produces minimal odor during printing. However, while it exhibits excellent strength and detail, its heat resistance is relatively low, making it unsuitable for applications exposed to high temperatures.
ABS (Acrylonitrile Butadiene Styrene) is renowned for its resilience and toughness. It can withstand higher temperatures than PLA and offers a more robust solution for functional prototypes. The downside of ABS is its tendency to warp during the cooling process, necessitating a heated print bed for optimal results. Furthermore, it emits fumes during printing, which necessitates adequate ventilation.
PETG (Polyethylene Terephthalate Glycol-Modified) combines the best features of both PLA and ABS, providing durability, ease of printing, and chemical resistance. PETG is suitable for creating functional parts or containers, though it can be slightly more challenging to adhere to the print bed without proper preparation.
Nylon is favored for its flexibility and strength, making it an excellent choice for parts that require durability and resistance to wear. Its hydrophilic nature can be a limitation as it absorbs moisture from the air, affecting its performance. TPU (Thermoplastic Polyurethane) offers elasticity, ideal for manufacturing parts that require flexibility, such as phone cases and seals. However, the printing process can be slower due to its soft nature.
Lastly, Resin printing allows for highly detailed and smooth finishes, suitable for intricate designs. Different types of resin cater to various applications, including flexible and high-temperature variants. However, this method can be more complex and often involves post-processing steps to achieve the desired results.
Assessing these common 3D printing materials — PLA, ABS, PETG, Nylon, TPU, and Resin — along with their properties, helps designers and engineers make informed decisions based on their project’s specific requirements and restraints.
Factors to Consider When Choosing 3D Printing Materials
When embarking on a 3D printing project, selecting the appropriate materials is a crucial step that significantly influences the final product’s quality and functionality. Several essential factors must be carefully considered to ensure the chosen material aligns with project requirements.
First and foremost, mechanical properties are paramount. Depending on the intended application, users should assess the strength, flexibility, and durability of the material. For instance, materials like ABS are known for their toughness, making them suitable for functional prototypes, while PLA is generally more rigid and may not withstand high-stress applications.
Secondly, thermal resistance plays a vital role, particularly in applications exposed to heat. It is necessary to understand the material’s glass transition temperatures and its ability to maintain structural integrity under various thermal conditions. This factor is especially critical for parts used in automotive or aerospace industries, where temperature fluctuations can occur.
Additionally, the environmental impact of the selected materials cannot be overlooked. With the growing emphasis on sustainable manufacturing practices, choosing eco-friendly materials, such as biodegradable PLA, can significantly enhance a project’s green credentials. Understanding the recyclability and disposal methods of materials is also essential for responsible sourcing.
Cost is a practical consideration that affects material selection. Budget constraints should be evaluated alongside performance needs, as premium materials may offer superior properties but also come at a higher price. It is important to balance quality and cost-effectiveness to avoid compromising on the project’s requirements.
Lastly, printability is a critical factor that addresses the ease of printing. Each material has specific conditions for optimal print results, including temperature settings, bed adhesion, and required supports. Some materials may require advanced printing techniques or equipment, making it essential to ensure compatibility with available resources.
Specific Applications and Material Choices
3D printing has revolutionized various industries by providing innovative solutions tailored to specific applications. When it comes to selecting the right materials for 3D printing, it is crucial to consider the intended use of the printed object. Prototyping, functional parts, and artistic creations each require distinct material properties to maximize performance and durability.
In the automotive sector, 3D printing is utilized for creating prototypes and end-use components. Materials such as ABS (Acrylonitrile Butadiene Styrene) and nylon are favored for their strength and flexibility. For example, companies like BMW employ nylon in prototyping because of its excellent durability and temperature resistance. Furthermore, the ability to create lightweight yet robust designs allows automotive engineers to innovate rapidly. This results in not only enhanced performance but also reduced production costs.
In the medical field, the choice of 3D printing materials is even more critical, as they directly affect patient safety and treatment outcomes. Medical applications often require biocompatible materials like PLA (Polylactic Acid) or even advanced polymers such as PEEK (Polyether Ether Ketone) for orthopedic implants. These materials offer not only the necessary mechanical properties but also the sterility required for surgical use. For instance, 3D printed custom prosthetics using these materials have shown remarkable results, enhancing comfort and fit for patients.
Similarly, in consumer products, the diversity of 3D printing materials allows for the design of unique and innovative items. Designers may opt for flexible TPU (Thermoplastic Polyurethane) for items that require elasticity, such as phone cases or wearable technology. By selecting appropriate materials, manufacturers can enhance functionality and aesthetic appeal, catering directly to consumer demands.
Thus, understanding the specific applications within which 3D printing materials will be used is fundamental to ensuring optimal selection. This consideration not only facilitates improved functionality but also contributes to the overall success of the project.
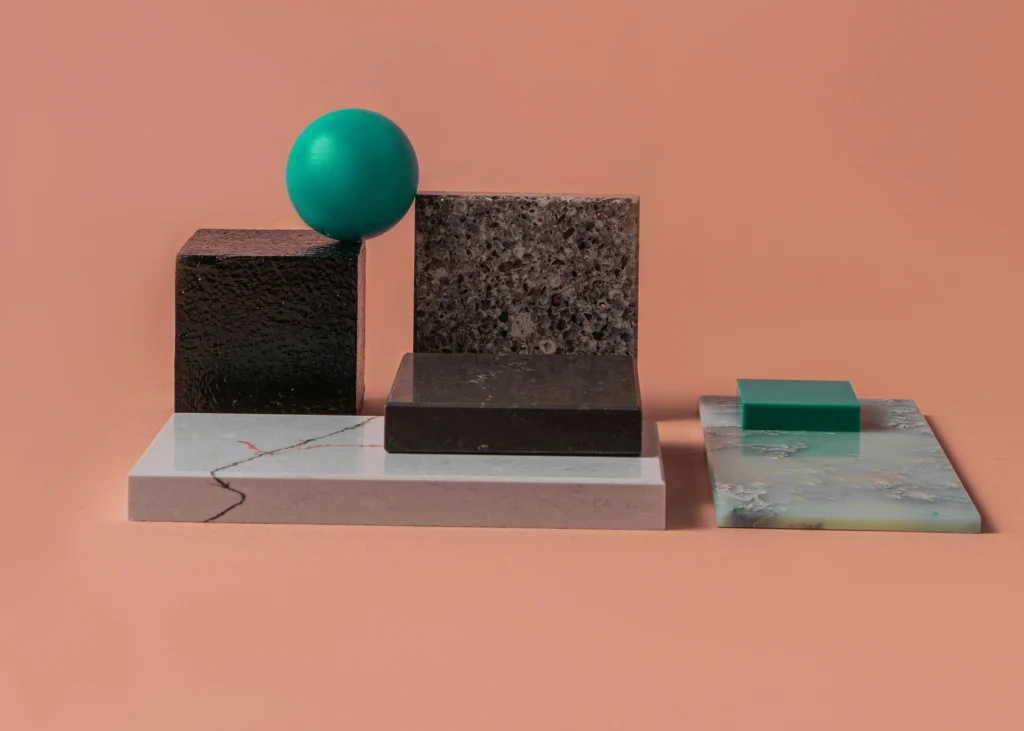
Advanced Materials for Specialized Applications
In the realm of 3D printing, the development of advanced materials has played a pivotal role in expanding the applications and functionality of printed objects. Among these, carbon fiber composites, metal filaments, and bio-based materials stand out for their unique properties and capabilities. Understanding when and why to incorporate these specialized materials is essential for achieving optimal results in various projects.
Carbon fiber composites are renowned for their remarkable strength-to-weight ratio, making them ideal for industries where lightweight and strong components are paramount, such as aerospace and automotive sectors. These materials consist of a matrix of plastic reinforced with carbon fibers, promoting enhanced performance while reducing overall weight. When high durability and stiffness are needed without the bulk, carbon fiber composites become an indispensable choice for engineers and designers.
Metal filaments represent another advancement in 3D printing technology, allowing for the production of parts that can withstand greater mechanical stresses and elevated temperatures. These materials can include stainless steel, aluminum, and even bronze, providing a level of resistance that is often required in industrial applications. Metal 3D printing is increasingly being utilized in industries such as tooling, automotive, and even healthcare, where strong performance and precision are critical.
Bio-based materials, on the other hand, cater to sustainability-focused projects and applications. Derived from renewable resources, these materials, such as PLA (polylactic acid), not only reduce carbon footprints but also offer biodegradability. They are suitable for prototyping, educational projects, and consumer products that prioritize environmental considerations. As the demand for sustainable solutions grows, bio-based materials present a compelling choice for projects needing to align with green practices.
The selection of an appropriate advanced material can greatly impact the efficacy of a project. Choices should be influenced by the specific requirements of the application, including mechanical properties, environmental factors, and the intended use of the final product.
Sourcing and Costs of 3D Printing Materials
When embarking on a 3D printing project, selecting the right materials is critical, and sourcing them effectively can significantly impact both the budget and the quality of the final product. There are several avenues available for sourcing 3D printing materials, including local suppliers, online retail platforms, and even recycling options. Each of these sources has its advantages and disadvantages, depending on factors such as availability, convenience, and cost.
Local suppliers often provide the advantage of immediate access to a variety of materials, allowing users to examine the products before making a purchase. Additionally, purchasing locally can facilitate quicker project turnaround, as shipping times can be circumvented. However, the selection offered by local suppliers may be limited compared to the vast options available online.
Online retailers are another valuable resource for 3D printing materials, offering a broader array of choices including specialty filaments, resins, and powders. These platforms can allow users to easily compare prices, read customer reviews, and find specific materials that fit their project requirements. It is important to factor in shipping costs and delivery time when budgeting for materials sourced online, as these elements can add unpredictability to the total expense.
In addition to traditional sourcing methods, recycling materials is an emerging trend in the 3D printing community. This approach not only reduces waste but can also lower material costs significantly. Various companies specialize in producing filaments made from recycled plastics, presenting an eco-friendly alternative for designers looking to minimize their environmental footprint.
Cost factors for 3D printing materials are influenced by several variables, including the type of material, its quality, and the manufacturer. High-quality materials often come at a premium, but investing in superior materials can provide enhanced performance and printability. By thoroughly evaluating these sourcing options and understanding the costs associated with them, project planners can more effectively budget for their 3D printing endeavors.
Testing Materials Before Full-Scale Printing
When embarking on a significant 3D printing project, it is vital to conduct thorough testing of materials before committing to full-scale prints. This process not only helps in understanding the material’s characteristics but also ensures compatibility with the 3D printer being used. Small test prints, or prototypes, are effective methods for assessing how different materials will perform in terms of strength, flexibility, and overall print quality.
One effective strategy for testing materials involves creating scaled-down versions of the intended print. This technique allows artists and engineers to evaluate the behavior of the material under real-world conditions without the waste associated with full-scale prints. During these small test prints, pay close attention to the printer settings, such as temperature and speed, as these can significantly affect the final product. Adjusting settings according to the material chosen can lead to optimal results and avoid costly errors.
Additionally, it is essential to analyze the physical properties of the printed test pieces. Inspect aspects such as layer adhesion, surface finish, and dimensional accuracy, and make notes of any anomalies. These evaluations help in making informed decisions regarding the suitability of a material for the desired project. Testing materials can also highlight any potential challenges related to integration, such as how well different materials bond and work together in composite prints.
It is equally important to ensure that the chosen material is compatible with the specific 3D printer. Compatibility issues can lead to printing failures and wasted resources. Manufacturers often provide guidelines on which materials work best with their printers, making it helpful to refer to these when selecting materials for testing.
Ultimately, verifying the characteristics of materials through testing can lead to more efficient and effective full-scale prints. By implementing these strategies, one can minimize waste and optimize results, ensuring the success of the 3D printing project.
Trends in 3D Printing Materials
The world of 3D printing is rapidly evolving, with constant advancements in materials that enhance the capabilities and applications of this innovative technology. One of the most notable trends in 3D printing materials is the development of new polymers and composites that provide improved strength, flexibility, and temperature resistance. These advancements allow designers and manufacturers to explore a broader range of applications, from aerospace components to medical implants. The ability to print more specialized materials is pushing the boundaries of what is possible in additive manufacturing.
Another significant trend is the utilization of bio-based and recycled materials in 3D printing. The increasing awareness of environmental concerns has led to a surge in the demand for sustainable materials. Manufacturers are now focusing on creating filaments made from biodegradable sources or recycled plastics. This shift not only minimizes waste but also encourages a more circular economy in the manufacturing sector. Innovations in biodegradable polymers and composites are also paving the way for more environmentally friendly products, making sustainability a key consideration for future material selections in 3D printing.
Moreover, advancements in print technology have enabled the use of multi-material printing, allowing for the incorporation of diverse material properties in a single print. This technique opens up new possibilities in creating complex geometries and functional parts that require different material characteristics. Techniques such as gradient printing and the development of printable electronics are also revolutionizing the field, resulting in integrated products that combine mechanical and electrical functions. As the industry continues to innovate, the focus remains firmly on materials that not only enhance performance but also cater to the growing demand for sustainability and efficiency in manufacturing processes.
Conclusion: Tailoring Your Material Choice to Your Project Needs
In the realm of 3D printing, selecting the appropriate material is paramount to achieving successful project outcomes. The versatility of 3D printing materials is a double-edged sword; while it offers a plethora of options, it also necessitates that users make informed choices tailored to their specific project requirements. Understanding the properties of various materials—such as PLA, ABS, PETG, and nylon—is crucial in determining their suitability for different applications.
In the previous sections, we discussed the implications of mechanical properties, thermal resistance, and ease of use, among other factors. For example, PLA is favored for beginners due to its user-friendly nature and environmental friendliness, while ABS is more suitable for applications requiring higher durability and heat resistance. Each material brings its own set of advantages and challenges, making it essential to align your choice with the intended application. Accurate assessment of functional requirements is key—whether your project demands flexibility, rigidity, or even biocompatibility.
Moreover, it is also important to consider post-processing options and the overall cost of materials. While some high-performance materials may promise superior results, they can also drive up project expenses. Therefore, a careful evaluation of budgetary constraints alongside the performance characteristics of materials is necessary for effective project planning. Always remember that the effectiveness of 3D printing hinges not only on the printer itself but equally on the material utilized.
By reviewing these critical aspects, we encourage readers to thoroughly explore their options and make educated decisions in their 3D printing endeavors. Ultimately, the right material can significantly enhance the quality, functionality, and success of the final product, paving the way for innovative outcomes in 3D printing projects.
Follow us on our Facebook page: Facebook
Click here to see our Work which consists of modern and functional websites that make a difference.